FAMED FORMULA 1 designer Gordon Murray has created another cool vehicle, but it’s not a race car. It’s a big, boxy truck that ships in pieces that go together just like that bookcase you bought at Ikea.
Murray designed the flat-pack truck, called the OX, for philanthropist Torquil Norman and his company, Global Vehicle Trust. The first prototype appeared in 2013. Three years, $4 million, and two prototypes later, the Trust has revealed a tested, more complete version.
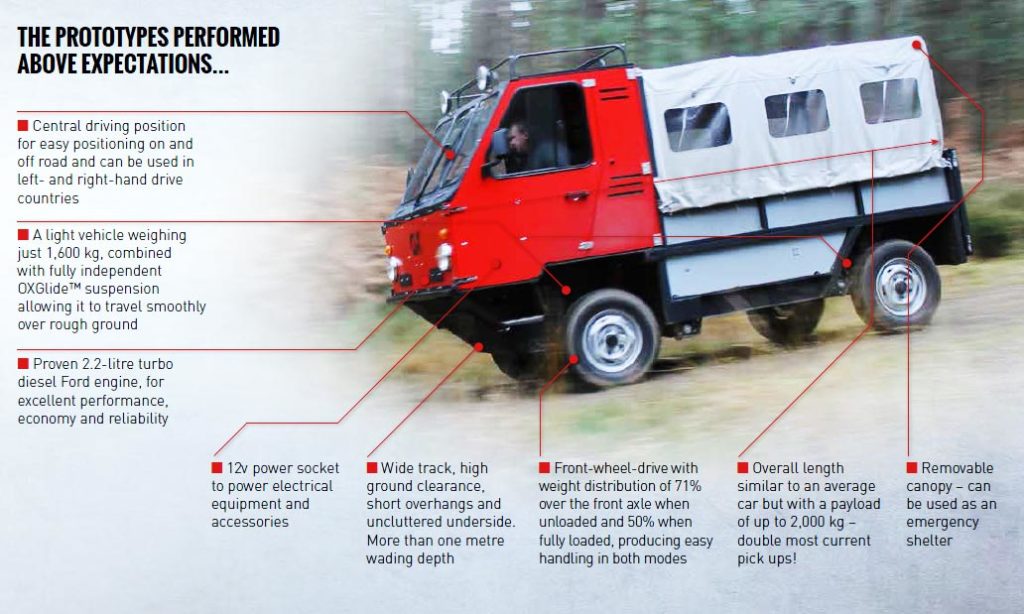
Inspiration for the OX came from the Africar, a lightweight, all-terrain vehicle that came and went in the mid-1980s. The flat-pack construction, however, is a first. “No one has done a flat-pack truck before, so the problems you need to solve are very different from anything like housing or furniture,” Murray says. “We really had to start from scratch.” That meant designing the truck in CAD and then iterating again and again on how to break it down and economically pack it together. The final OX prototype comes in about 60 pieces, Murray says.
And the idea is brilliant: A flat-pack vehicle, much like flat-pack furniture, requires less space for shipping. (A 40-foot shipping container can hold six flat-packed trucks but just two assembled trucks.) That makes it easier and cheaper to send trucks to Africa—OX’s initial market—where reliable ground transportation is a scarce and valuable resource.
The company claims three people can build an OX in just 12 hours. That’s thanks to user-friendly touches like the windshield, which features three identical panels that are easily assembled and replaced. The OX’s ground clearance and 45 degree approach- and departure-angle let it tackle the roughest roads. Top Gear called the truck unbreakable, and applauded its smooth ride. And there’s plenty more: OX’s website compares the trucks specs to those of a 4×4 cab truck and a 4×4 passenger vehicle—the OX bests them both on multiple fronts.
The OX, for example, is much lighter than the average truck because of Murray’s iStream manufacturing method. His radical approach aims to upend vehicle manufacturing by replacing stamped steel unibodies with honeycomb tube steel frames coated in composite materials like fiberglass, polyurethane, and paper. The OX, however, has drastically different needs. “We couldn’t use the standard iStream as the material because the sort of abuse a truck gets in Africa—like dropping a 44-gallon drum of water onto it from a couple of meters up—it’s just going to punch a hole in the composite panel.” Instead, the OX uses a waterproof bonded wood composite. Murray and his team found the material, known as Scandinavian engineered plywood, or Wisa board, after a global search for a durable but lightweight material. Wisa board gets used on children’s playgrounds and in the backs of trucks that carry wet gravel out of quarries—strong stuff. Whether with composite steel or plywood, if the iStream technique takes off, Murray says it would fundamentally alter the way cars are made.
That’s a bold claim from a brilliant thinker, but when WIRED talked to Murray about iStream in 2011, he said this technique could make cars 20 to 25 percent lighter and 60 percent more efficient to manufacture. The OX is the closest Murray has come to a proof of concept—but it’s still got a ways to go. GVT has estimated it’ll need another $4 million to get OX trucks out into the world, but Murray says that figure just explains the cost needed to get a low volume number of humanitarian trucks into Africa. Murray sees broader potential. “There’s definitely a much bigger global market—there are certainly markets in China, Southeast Asia,” he says. “Now that we’ve benchmarked it, we also feel there’s a huge market for the truck in the developed world, for the farming community.” Another bold claim from a bold thinker.
Source: Wired